Keep the weather outside this year...where it belongs
Damaged Insulation Removal for the Akron Area and surrounding neighborhoods
We remove old, damaged, and failing insulation from homes and businesses in Akron
What types of damage can occur to insulation? How often should insulation be replaced? As soon as you notice failures or spot damage!
We are positioned for a lot of bad weather here in northeast Ohio. We get lake effect snow, winds blowing off Lake Erie, and scorching summertime heat. Each of these can have a negative effect on homes and the insulation inside of them. Water, bugs, mold and time are the top destroyers of insulation, and many types of insulation are susceptible to fire damage. While some are treated against bugs, they cannot always prevent mold or water damage, and nothing can defeat plain old age. There are special paints called intumescent coatings, that can be applied to certain types of insulation to give it some fire resistance, these aim to prevent damage from small fires.
Damaged insulation brings a host of other problems with it including mold blooms, rotten wood beams, and off-color, even soggy drywall. If not caught and taken care of the damage will spiral out of control.
Remove Old Insulation
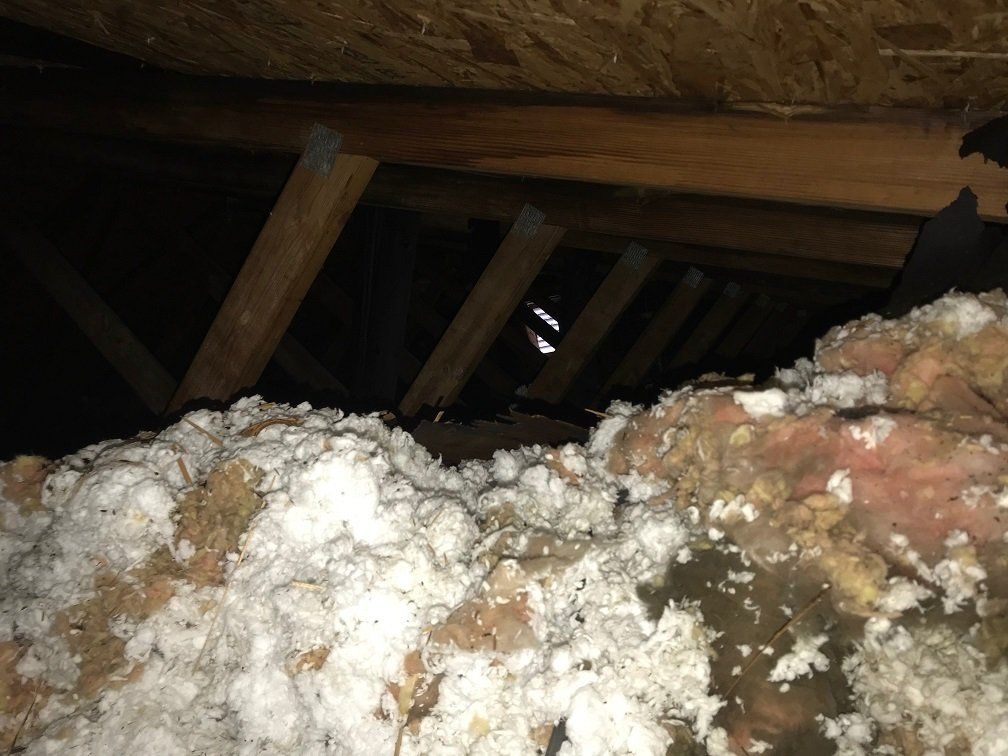
Lets go over the main types of damage to insulation
Water Damaged insulation: Damage from water will cause some insulations to lose their air trapping abilities. Fiberglass batts and loose fill insulations made from cellulose or fiberglass will collapse into a wet mess because they rely on trapped air to stop cold from creeping in. Other types are treated against water, such as rigid foam boards with a water-resistant core, and mineral wool insulation, which does not absorb water in any way. These will resist a lot of the damage from water and moisture, provided the water has a place to escape. The clear winner here is closed cell spray foam insulation, it is the only type of insulation that is considered fully waterproof.
Bug infestations in insulation:
These critters enter the home in much the same way that water does, through holes that lead to the outside. Bugs and critters both eat and make nests in insulation, its common to find mice bedding made from fiberglass insulation fluff because they want to be warm too. Bugs that hunker down in your attic insulation make bug families and that is another problem! Cellulose blown in insulation is treated against bugs with boric acid, which will either kill or deter critters from moving in. Mineral wool insulation is inorganic and tough, so bugs do not eat it and nesting is difficult. Spray foam insulation takes care of the problem by sealing air gaps where bugs enter the home to begin with. Mineral wool and spray foam insulation take the win in the bug prevention category.
Mold growth in insulation: Mold spores require water to grow, eventually colonizing, and mold prospers in damp, dark places. When mold has colonized, it is visible to the naked eye and is actively growing daily (see the image at the top to see colonized mold). This will happen approximately 18 days after the exposure. Insulation is often found in dark places, being inside a wall, or spread out in an attic and this makes it prime real estate for mold to grow on wet insulation. Untreated leaks in home siding or roofing dampens insulation and invites mold growth. Ideally, all insulation has a vapor barrier to help stop vapors bringing in mold spores, but these are not waterproof, and a leak will easily overcome most vapor barriers. There are products treated against mold growth like rigid foam boards. For complete prevention, mineral wool insulation and spray foam insulation do not promote mold growth at all and again are the clear winners for mold prevention.
Age of insulation: It’s a law of the universe, that all things go from order to disorder and break down over time. Insulation likewise has a lifespan and over time it may not provide its top R-value. Each insulation material has a different length of time they are most effective, some last longer than others. Let’s break down each type...
- Spray foam Insulation: Long lifespan of 80 years for open cell spray foam to 100 years for closed cell spray foam. Will not fall away from where applied during this period and homeowners will not need to replace it during their lifetime.
- Fiberglass insulation: Fiberglass has a long, but fragile lifespan. The fiberglass itself can last from 80 to 100 years, but the insulation can fall away from the batting within 15 to 20 years, even when undamaged. If damaged by water and subsequent mold, it will need to be completely replaced.
- XPS Foam Board Insulation: Extruded polystyrene boards contain gasses, called blowing agents, inside of trapped air pockets and these escape over time, trading the gas that should be present for regular old air. When this happens, the R-value of the insulation drops. Not to a rate where it is completely ineffective, but not the manufacturer stated R-value. The time span of this happening is not exact, manufactures keep much of this a trade secret, but on average, after 25 years about 90% of the blown gasses have been replaced by normal air.
- EPS foam board insulation: Expanded polystyrene is a foam board that is filled with pockets of normal air, because of this there is no opportunity to lose its blowing agent over time. EPS foam boards have a life span of 50 years when undamaged.
- Cellulose loose fill insulation: Because cellulose insulation is made from mostly recycled paper, it has a rather short and potentially delicate lifespan, lasting between 20 and 30 years. However, sources say that cellulose insulation can begin to break down in as little as 15 years because it is highly vulnerable to natural compression by gravity.
- Mineral Wood insulation: Mineral wool supplier, ROCKWOOL, says that their products last 50 years at a minimum and most other studies show a similar range of 50+ years when no damage has occurred. Mineral wool does not degrade in performance over time unless damaged.
To sum it up
Damaged and/or degraded insulation is not doing a proper job of insulating and should be replaced to increase the comfort of the occupants and longevity of the building. A visual inspection can help to target areas of concern and noticing the signs of damaged insulation while inside: Particularly cold rooms or areas indoors, signs of bugs or rodent activity, signs of mold growth, and cranking the thermostat more often than is normal.
If you suspect (or know!) that your insulation is damaged,
give us a call
(330) 352-4456, or
send us a message
to get a technician out for a free inspection and quote on insulation removal and new insulation installation.